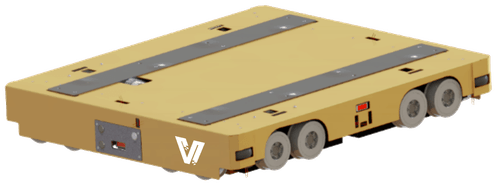
4-Way Shuttle
Introduction to 4-Way Shuttles in Warehouse Automation
Warehouse automation has transformed the logistics landscape, and among the most innovative solutions is the 4-way shuttle system. These systems have revolutionized inventory handling by offering flexibility, efficiency, and speed in operations. This document covers various aspects of 4-way shuttles, from their design and working principles to their applications, advantages, challenges, and future trends.
What is a 4-Way Shuttle?
A 4-way shuttle is a type of automated storage and retrieval system (AS/RS) designed to move goods within a warehouse. Unlike traditional shuttles that can only move in one or two directions, a 4-way shuttle can navigate both horizontally and vertically, allowing it to access four different orientations within racking systems. This design enhances operational efficiency by minimizing the need for additional machinery and reducing travel time within the warehouse.
Design and Components of a 4-Way Shuttle
1. Shuttle Vehicle:
- The shuttle itself is a compact vehicle equipped with wheels or tracks that allow it to navigate through a vertical racking structure.
- The 4-way shuttle is designed to move in four directions—left, right, forward, and backward—enhancing its operational flexibility.
2. Control System:
- The shuttle operates through a sophisticated control system, usually integrated with Warehouse Management Systems (WMS). This system manages tasks like routing, scheduling, and inventory tracking.
- Advanced control systems are often backed by Artificial Intelligence (AI) and Machine Learning (ML) capabilities, enabling dynamic optimization of operations.
3. Racking Structure:
- The racking system, designed to accommodate 4-way shuttles, typically includes vertical and horizontal storage slots.
- These racks maximize vertical space, allowing for increased storage within smaller footprints.
4. Load Handling Mechanism:
- Most 4-way shuttles are equipped with load handling features, such as lifts or forks, to pick up and deposit goods efficiently.
- This mechanism may vary depending on the type of products being handled, ensuring compatibility with different sizes and shapes of inventory.
5. Communication Infrastructure:
- A robust communication network includes sensors, cameras, and RFID systems, which help the shuttle navigate and track inventory in real-time.
Operating Principle of 4-Way Shuttles
The operation of a 4-way shuttle involves several key steps:
Inventory Management:
- The WMS continuously monitors inventory levels and types, prompting the shuttle to retrieve or deposit goods as needed.
Task Assignment:
- Based on the WMS instructions, tasks are assigned to the shuttle, determining its route and the storage location of products.
Navigation:
- Combining onboard sensors and real-time data, the shuttle navigates efficiently through the storage structure, adapting its path according to obstacles or changes in demand.
Load Handling:
- Once the shuttle reaches the designated storage location, its load handling mechanism picks up or deposits the goods.
Return and Reporting:
- After completing its task, the shuttle returns to a designated station, updating the WMS about its task completion and current inventory status.
Applications of 4-Way Shuttles
4-way shuttles are versatile and can be utilized in various sectors:
E-commerce Warehouses:
- With the increasing demand for quick order fulfillment, e-commerce platforms rely on 4-way shuttles for speedy retrieval and packing processes.
Manufacturing:
- In manufacturing settings, 4-way shuttles transport components between different stages of production, enhancing workflow and reducing downtime.
Food and Beverage Industry:
- Temperature-controlled 4-way shuttles are vital for transporting perishables efficiently while adhering to safety standards.
Pharmaceuticals:
- In the pharmaceutical industry, precise control and tracking of inventory are crucial, and 4-way shuttles offer a high degree of accuracy and traceability.
Retail Supply Chains:
- Retailers utilize 4-way shuttles in distribution centers to manage large volumes of products efficiently, ensuring swift delivery to stores.
Advantages of 4-Way Shuttles
Increased Throughput:
- 4-way shuttles enhance inventory handling speed, contributing to higher throughput rates and faster order fulfillment.
Space Efficiency:
- The vertical design of the racking system paired with 4-way shuttle capability maximizes the use of available space in warehouses, allowing for more products to be stored in a smaller footprint.
Flexibility:
- With the ability to move in four directions, these shuttles can adapt to various workflow processes and inventory management needs with ease.
Reduced Labor Costs:
- Automating the storage and retrieval of goods through shuttles significantly reduces the labor needed, minimizing operational costs while improving workflow efficiency.
Enhanced Accuracy:
- Automated systems like 4-way shuttles significantly reduce human errors in inventory handling, providing higher accuracy in tracking and order fulfillment.
Scaling Capabilities:
- As demand grows, adding additional shuttles or expanding the racking system can often be accomplished with minimal disruptions to operations.
Challenges in Implementing 4-Way Shuttles
While 4-way shuttles offer numerous advantages, there are challenges associated with their implementation:
High Initial Investment:
- The initial costs for setting up a 4-way shuttle system can be substantial, including the costs for shuttles, racking systems, and control software.
Integration with Existing Systems:
- Integrating shuttle systems into current warehouse operations can be complex and may require reconfiguration of existing workflows or processes.
Maintenance and Technical Support:
- Automated systems require ongoing maintenance and skilled personnel to manage and troubleshoot issues, which can incur additional costs.
Space Constraints:
- Although 4-way shuttles optimize vertical space, implementing them may require considerable modifications to existing facilities, particularly for older infrastructure.
Change Management:
- Transitioning to an automated system can lead to resistance among employees who are concerned about job security or the learning curve associated with new technology.
Future Trends in 4-Way Shuttle Technology
AI and Machine Learning:
- Continued advancements in AI and ML will enable shuttles to learn from historical data and optimize routes dynamically, minimizing downtime and increasing efficiency.
Collaborative Robots (Cobots):
- The integration of 4-way shuttles with cobots may provide solutions for tasks requiring greater dexterity or human-like behavior, enhancing operational capabilities.
Sustainability:
- As companies focus on sustainability, manufacturers are likely to develop energy-efficient shuttles and racking systems that reduce the carbon footprint.
IoT Integration:
- The Internet of Things (IoT) will foster a more interconnected warehouse environment, enabling real-time data sharing and predictive maintenance capabilities for shuttles.
Customization:
- As warehouse needs evolve, the demand for customizable 4-way shuttle systems that align with specific operational requirements will increase.
Conclusion
4-way shuttles represent a transformative force in warehouse automation, offering significant advantages in efficiency, adaptability, and space utilization. By automating the storage and retrieval process, they lay the groundwork for modern supply chain operations, enabling companies to meet the ever-growing demands of consumers and businesses alike. Despite the challenges in implementation, the future of 4-way shuttle technology looks promising, with continuous advancements in AI, IoT, and robotics paving the way for more innovative and sustainable solutions in logistics. Organizations that effectively integrate 4-way shuttle systems into their operations are likely to experience enhanced productivity, cost savings, and the ability to remain competitive in an increasingly automated world.