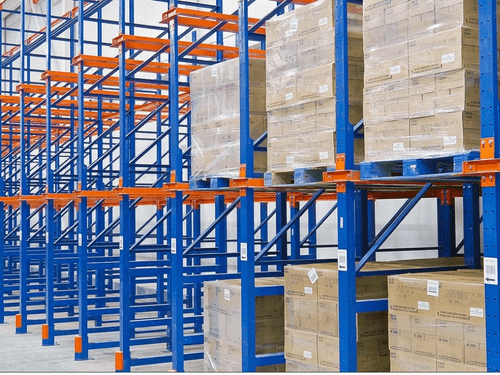
Drive in or Drive through rack
Introduction: Drive-in racks are a popular type of high-density storage solution used in warehouse environments to maximize storage capacity and operational efficiency. These racks are known for their unique design that allows forklifts to enter the storage lanes and retrieve or deposit pallets from either side of the rack structure. Drive-in racks are ideal for storing large quantities of the same SKU (Stock Keeping Unit) or products with low turnover rates. In this comprehensive guide, we will explore all aspects of drive-in racks, including their structure, surface treatment, function, usage, design considerations, advantages, and challenges.
Structure of Drive-In Racks: Drive-in racks are typically constructed using upright frames, load beams, support rails, and guide rail systems. The upright frames serve as the vertical supports of the rack structure and are anchored to the warehouse floor for stability. Load beams are horizontal components that span between the upright frames to support pallets and provide structural integrity to the rack system. Support rails are installed along the length of the storage lanes to guide the forklifts and ensure smooth pallet movement within the rack structure. Guide rail systems are often used to align the forklifts and prevent damage to the rack components during loading and unloading operations.
The design of drive-in racks allows for pallets to be placed directly on the load beams within the storage lanes, with each lane accommodating multiple pallets in a last-in, first-out (LIFO) configuration. Forklifts can drive into the storage lanes from one end of the rack system and retrieve or deposit pallets by moving along the designated paths within the rack structure. This design maximizes storage density by reducing aisle space and utilizing vertical space effectively, making drive-in racks an excellent choice for storing large quantities of homogeneous products.
Surface Treatment of Drive-In Racks: Surface treatment plays a critical role in enhancing the durability, corrosion resistance, and aesthetic appeal of drive-in racks. Common surface treatment options for drive-in racks include powder coating, galvanization, and enamel paint. Powder coating is a popular choice for its durability, environmental friendliness, and resistance to chipping, scratching, and fading. Galvanization involves the application of a protective zinc coating to the steel components of the rack structure, providing excellent corrosion resistance and longevity in harsh environments. Enamel paint is often used for aesthetic purposes, allowing for customization of the rack color to match the warehouse decor or branding.
Proper surface treatment not only protects the drive-in racks from wear and tear but also ensures a clean and professional appearance, contributing to a safe and organized warehouse environment. Regular maintenance and inspection of the surface treatment are essential to prolong the lifespan of drive-in racks and maintain their structural integrity under heavy load conditions.
Function and Usage of Drive-In Racks: The primary function of drive-in racks is to provide efficient and high-density storage for palletized goods in warehouse settings. These racks are commonly used in industries with large inventory volumes, low SKU diversity, and limited space availability. Drive-in racks are well-suited for storing products with long shelf lives, bulk items, seasonal goods, and slow-moving inventory that can be kept in storage for extended periods without frequent retrieval.
The unique design of drive-in racks allows forklifts to access multiple pallet positions within the storage lanes, eliminating the need for aisles between rack rows. This feature maximizes storage capacity by utilizing the available space effectively and reducing wasted floor area dedicated to aisles. Drive-in racks are especially beneficial for facilities with limited space or high land costs, as they maximize vertical storage and enable efficient use of the warehouse footprint.
Design Considerations for Drive-In Racks: When designing a drive-in rack system, several key considerations should be taken into account to optimize its performance and functionality:
- Pallet Dimensions and Weight: Determine the size and weight capacity of the pallets to be stored in the drive-in racks to configure the rack structure and load beams accordingly.
- Aisle Width and Clearance: Plan the width of the aisles between drive-in rack rows to accommodate the forklifts and ensure safe and efficient pallet handling operations.
- Load Capacity and Beam Spacing: Calculate the load capacity of the drive-in racks and the spacing between load beams to support the intended pallet loads and prevent overloading.
- Rack Height and Configuration: Determine the height of the drive-in racks based on the warehouse ceiling clearance and the vertical storage capacity required for the pallet inventory.
- Drive-In Entry and Exit Points: Design the entry and exit points for the forklifts to access the storage lanes and maneuver within the rack structure without obstruction.
- Safety Features: Incorporate safety features such as impact guards, aisle end protectors, rack frame protectors, and warning signs to prevent accidents and protect personnel and equipment during forklift operations.
Advantages of Drive-In Racks: Drive-in racks offer numerous benefits for warehouse and distribution operations, including:
- High Storage Density: Drive-in racks maximize storage capacity by eliminating aisles between rack rows and utilizing vertical space effectively to store large quantities of palletized goods.
- Cost Savings: By maximizing storage density and reducing aisle space requirements, drive-in racks help reduce the overall footprint of the warehouse and lower operating costs associated with land, rent, and utilities.
- Increased Throughput: The efficient design of drive-in racks allows forklifts to access multiple pallet positions within the storage lanes, speeding up pallet retrieval and deposition processes for improved operational efficiency.
- Inventory Control: Drive-in racks provide easy access to stored pallets and enable systematic inventory management, tracking, and rotation to ensure accurate stock levels and minimize stockouts.
- Improved Space Utilization: Drive-in racks optimize the use of available space by utilizing vertical storage and reducing wasted floor area, enabling warehouses to accommodate more inventory within the same footprint.
- Customizable Configurations: Drive-in racks can be customized and configured to meet specific storage requirements, such as varying pallet dimensions, load capacities, and aisle widths, to adapt to changing inventory profiles and operational needs.
Challenges and Considerations: Despite their advantages, drive-in racks also present challenges and considerations that should be addressed when implementing this storage solution:
- Limited Selectivity: Drive-in racks have limited selectivity for accessing individual pallets within a storage lane, as they operate on a last-in, first-out (LIFO) basis, which may not be suitable for fast-moving or perishable goods that require frequent access.
- Load Balancing: Proper load balancing within the drive-in racks is essential to prevent overloading, maintain structural integrity, and ensure safe operation of the rack system.
- Forklift Compatibility: Drive-in racks require specialized forklifts with narrow aisle capabilities and extended reach to navigate the storage lanes and retrieve pallets safely, which may require additional training and equipment investment.
- Temperature Control: Drive-in racks may not be suitable for temperature-sensitive goods or refrigerated storage applications, as the limited airflow and accessibility within the storage lanes could impact product quality and shelf life.
- Maintenance and Repair: Regular maintenance and inspection of drive-in racks are necessary to address wear and tear, damage, and structural issues that may affect the safety and functionality of the rack system.
Conclusion: Drive-in racks are a versatile storage solution that offers a high-density storage option for warehouse facilities looking to optimize storage space, increase operational efficiency, and streamline inventory management. By understanding the structure, surface treatment, function, usage, design considerations, advantages, and challenges of drive-in racks, organizations can make informed decisions when implementing this storage solution in their facilities. With proper planning, configuration, and maintenance, drive-in racks can enhance warehouse storage capabilities, improve inventory control, and support the overall operational success of modern supply chain environments.