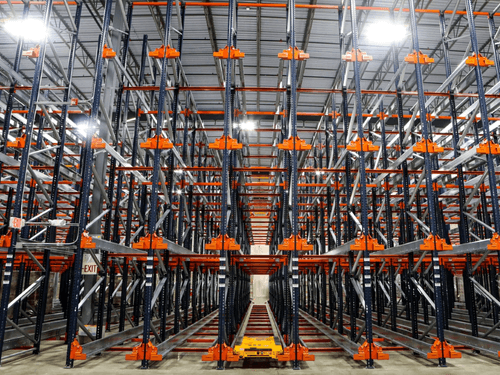
Shuttle rack
Shuttle racks, also known as shuttle car racks or pallet shuttle systems, are a type of high-density storage solution used in warehouses and distribution centers to optimize space utilization and improve operational efficiency. The shuttle rack system integrates automated shuttle vehicles to transport and retrieve pallets within the rack structure, eliminating the need for forklifts to enter the racks for pallet handling. This innovative design maximizes storage capacity, increases throughput, and enhances inventory management capabilities.
Structure of Shuttle Racks: Shuttle racks consist of a series of racking bays, typically supported by upright frames and cross beams, arranged in rows with aisles in between for shuttle vehicle access. These racks are designed to accommodate pallets of various sizes and weights, with configurations tailored to the specific requirements of the facility. The shuttle vehicles, also known as shuttles or carriers, are battery-powered devices equipped with a platform for pallet transport along the rails or tracks installed within the rack structure. The shuttle system is controlled by a central management software that coordinates the movement of the shuttles, ensuring efficient pallet storage and retrieval operations.
Surface Treatment of Shuttle Racks: The components of shuttle racks, such as upright frames, cross beams, and shuttle vehicles, are typically treated with various surface coatings to enhance durability, resistance to corrosion, and aesthetic appeal. Common surface treatment options for shuttle racks include powder coating, galvanization, and epoxy coating, which provide protective layers against wear and tear, environmental factors, and chemical exposure. These surface treatments contribute to the longevity and performance of shuttle racks in demanding warehouse environments.
Function and Usage of Shuttle Racks: The primary function of shuttle racks is to maximize storage density and operational efficiency by automating pallet handling tasks within the rack structure. The shuttle vehicles travel along the rails to transport pallets to and from designated storage locations, eliminating the need for manual pallet movement and reducing labor costs. Shuttle racks are commonly used in industries with high-volume storage and throughput requirements, such as food and beverage, logistics, retail, and manufacturing. They are ideal for storing perishable goods, fast-moving inventory, and bulk items that require rapid access and replenishment.
Design Considerations for Shuttle Racks: When designing a shuttle rack system, several factors should be taken into consideration to ensure optimal performance and functionality:
- Pallet Size and Weight: Determine the dimensions and weight capacity of the pallets to be stored in the shuttle racks to select the appropriate rack configuration and shuttle vehicle specifications.
- Rack Layout and Configuration: Plan the layout of the rack structure, including aisle widths, storage heights, and shuttle vehicle travel paths, to maximize storage capacity and operational efficiency.
- Shuttle Vehicle Technology: Choose the right type of shuttle vehicles based on the storage requirements, such as single-deep or double-deep storage, speed capabilities, payload capacity, and battery life.
- Integration with Warehouse Management System: Integrate the shuttle rack system with the existing warehouse management software for seamless pallet tracking, inventory control, and order fulfillment processes.
- Safety Features: Implement safety features such as collision avoidance systems, emergency stop buttons, and light curtains to ensure the safe operation of shuttle racks and protect personnel and equipment from accidents.
- Scalability and Flexibility: Design the shuttle rack system with scalability and flexibility in mind to accommodate future expansion, changes in inventory profiles, and evolving operational needs.
Advantages of Shuttle Racks: Shuttle racks offer numerous advantages for warehouse and distribution operations, including:
- Increased Storage Capacity: Shuttle racks maximize storage density by utilizing vertical space and reducing aisle width requirements, allowing for more efficient use of available floor space.
- Improved Throughput: The automated shuttle system speeds up pallet storage and retrieval processes, reducing handling time and increasing the overall throughput of the warehouse.
- Space Optimization: Shuttle racks optimize space utilization by eliminating wasted aisle space and allowing for efficient organization of inventory based on storage requirements.
- Inventory Accuracy: The centralized management software of shuttle racks provides real-time inventory visibility, accuracy, and control, minimizing errors in picking, stocking, and inventory tracking.
- Labor Savings: By automating pallet handling tasks, shuttle racks reduce the reliance on manual labor for repetitive and time-consuming warehouse operations, leading to cost savings and increased productivity.
- Redundancy and Reliability: Shuttle rack systems are designed with redundancy and fail-safe mechanisms to ensure reliable operation and minimize downtime in the event of component failures or system malfunctions.
- Energy Efficiency: Shuttle racks utilize energy-efficient shuttle vehicles and optimize travel paths within the rack structure, reducing energy consumption and operating costs compared to traditional storage systems.
Challenges and Considerations: While shuttle racks offer numerous benefits, there are also challenges and considerations to keep in mind when implementing this storage solution:
- Initial Investment: Shuttle rack systems require a significant upfront investment in infrastructure, technology, and software, which may pose a financial barrier for some organizations.
- Maintenance and Repairs: The automated components of shuttle racks, such as shuttle vehicles and control systems, require regular maintenance and occasional repairs to ensure optimal performance and longevity.
- Training and Skill Requirements: Operating and managing a shuttle rack system may require specialized training for personnel to effectively handle and troubleshoot the automated components and software.
- System Integration: Integrating a shuttle rack system with existing warehouse infrastructure, material handling equipment, and software systems may require careful planning and coordination to ensure a seamless transition and minimal disruptions to operations.
- Scalability and Expansion: Consider future growth projections and operational changes when designing a shuttle rack system to accommodate scalability and expansion requirements without significant redesign or investment.
Conclusion: Shuttle racks are an innovative storage solution that combines automation, efficiency, and space optimization to streamline warehouse operations and enhance inventory management capabilities. By understanding the structure, surface treatment, function, usage, design considerations, advantages, and challenges of shuttle racks, organizations can make informed decisions when implementing this technology in their facilities. With proper planning, configuration, and maintenance, shuttle racks can revolutionize warehouse storage, improve efficiency, and drive operational excellence in today's fast-paced and dynamic supply chain environments.